Well, recently I went to a veterans sponsored car show out here in Loma Linda. First time visiting the event and I was really impressed with the setup and layout.
Web site said they cap the registered limit at around 1000 cars. Not sure there were that many but it was quite substantial.
I plan on being more than a spectator for next year.
That is my lead in for hearing constantly from friends and family the "you should enter your car" statment. 1000 cars and there was only one other Challenger. Many of the others I attend local also never have a single Challenger in them.
So...
I did a lot of cleaning, replacing and touching up of my car this last week so I could enter another one close to home in Placentia. Much smaller, probably 200-300 cars.
From my earlier engine bay postings I realized it was also in need.
View from previous mock up for visual.
And the now.
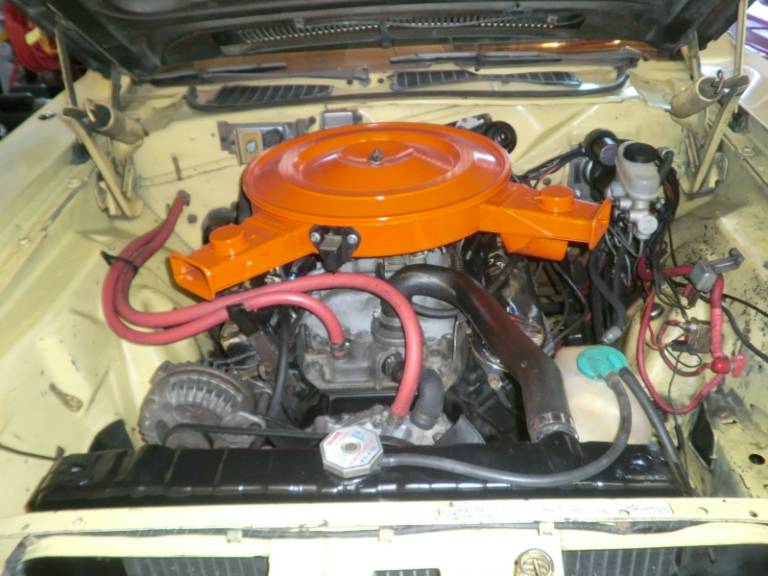
Will still eventually need to repair this damage from an unfortunate hit with a large dog (RIP).
Have had a replacement for this for a long time but never put it in.
Here is the replacement grill cleaned and installed. Still will need to replace the surrounding strip trim. I just pounded it out a bit so it will at least be close to the correct shape.
Worked on the back also to clean it up.
Before:
And after. The idea was not to restore it. Just to remove several years of wear.
Painted the light recesses. Paint did not come out as flat as I would have liked. It is more of a low sheen semi gloss.
Also did some small fogging sprays of silver to lessen the reddish primer showing through.
I really like the tone of the argent that this car has. So all improvements will be as minor as possible so when the real restoration happens I will still have visual enough remaining for them to replicate.
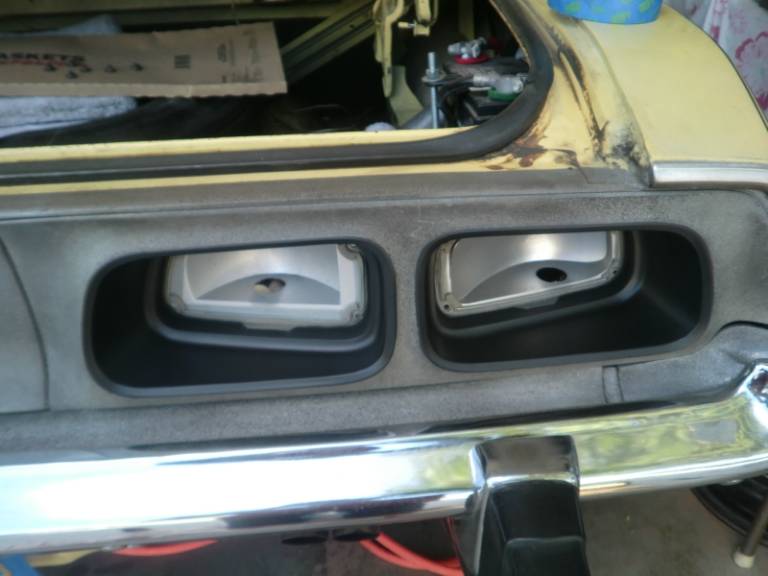
With lenses cleaned up:
A month or so ago I made a new package tray cover out of press board. This was also installed this past week.
102 holes drilled from both sides to prevent blowout later:
Covered in black cloth to hide the tunes holes.
Held together with contact cement:
Placentia show was good. Didn't win anything (seemed like an early Imap@!@ bias) but finally there was a Challenger represented...
After all that work I even forgot to take pictures of it at the show. dumb@$$.
Still good though.